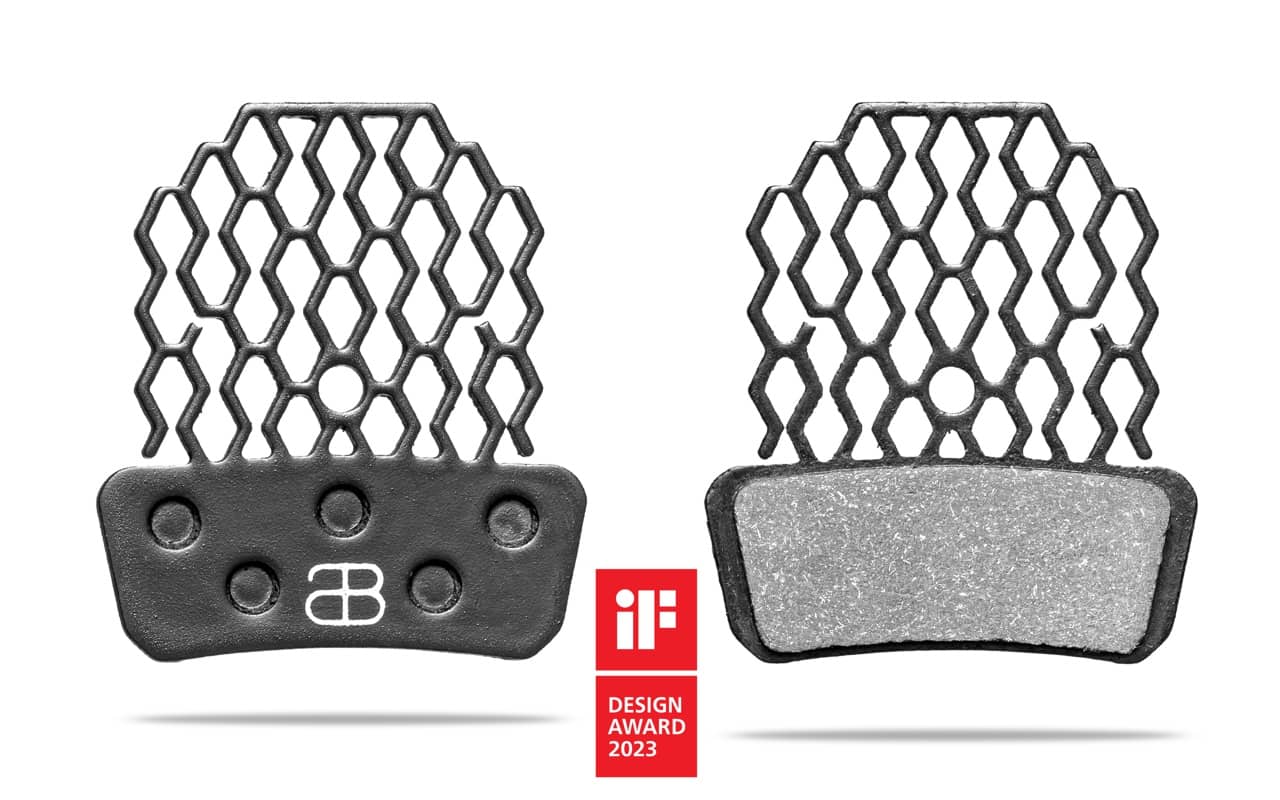
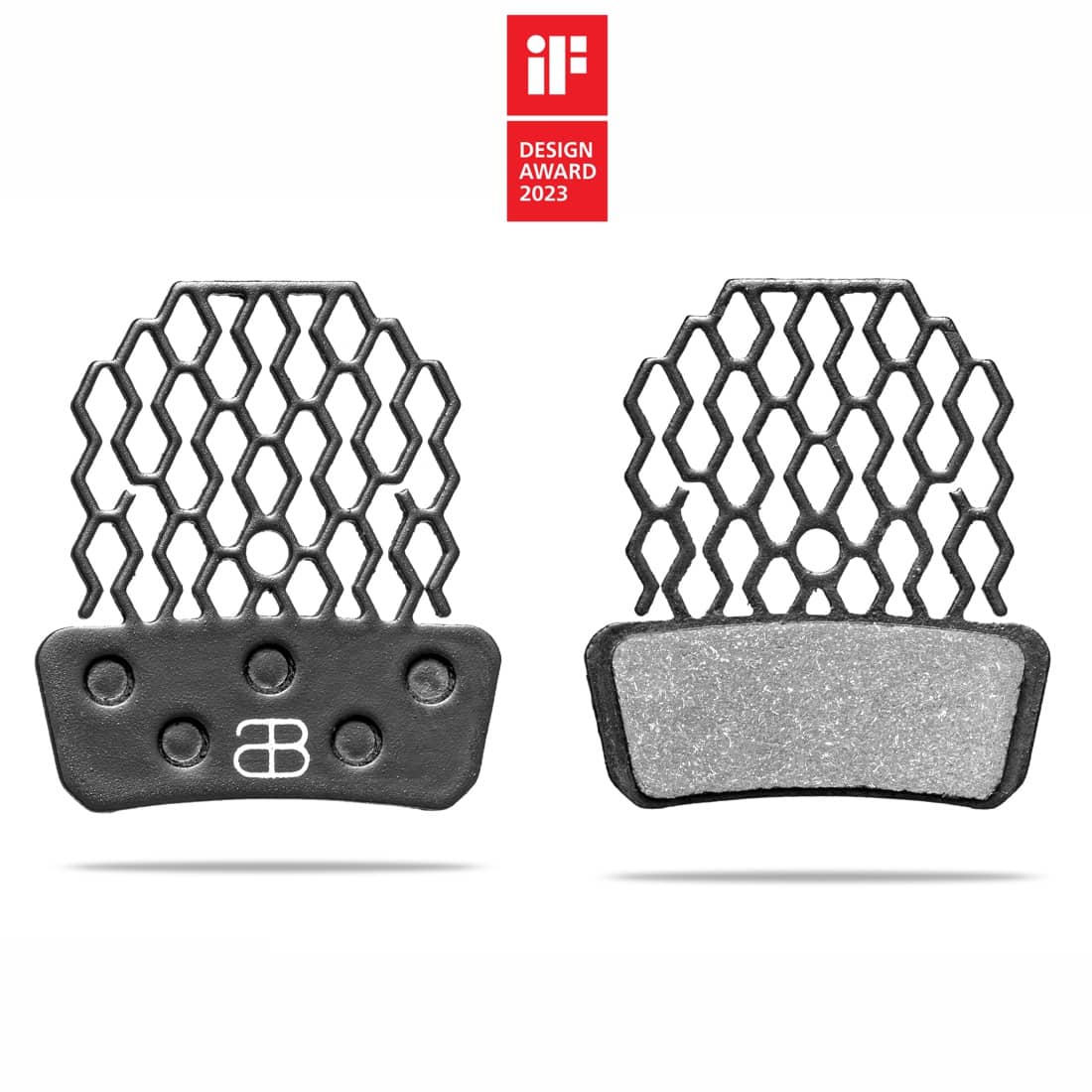
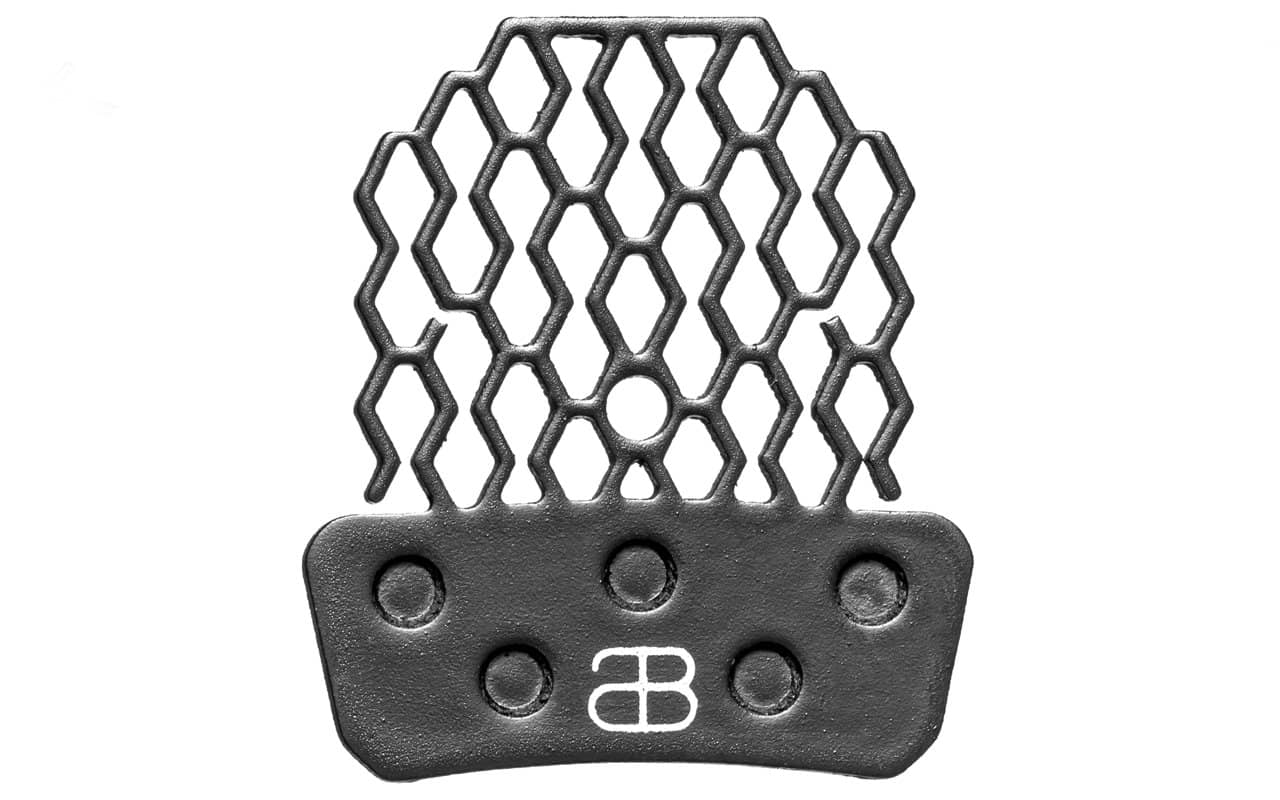
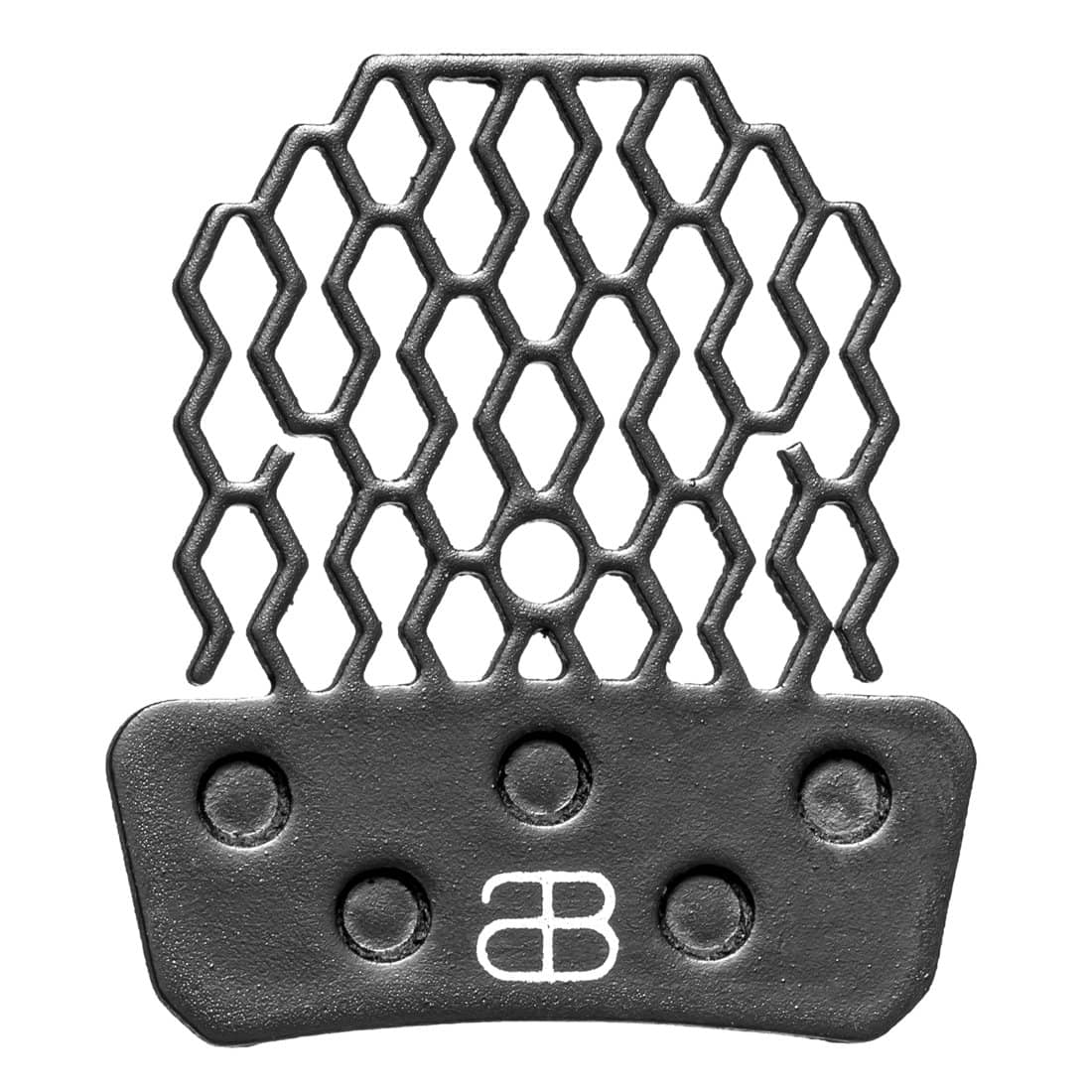
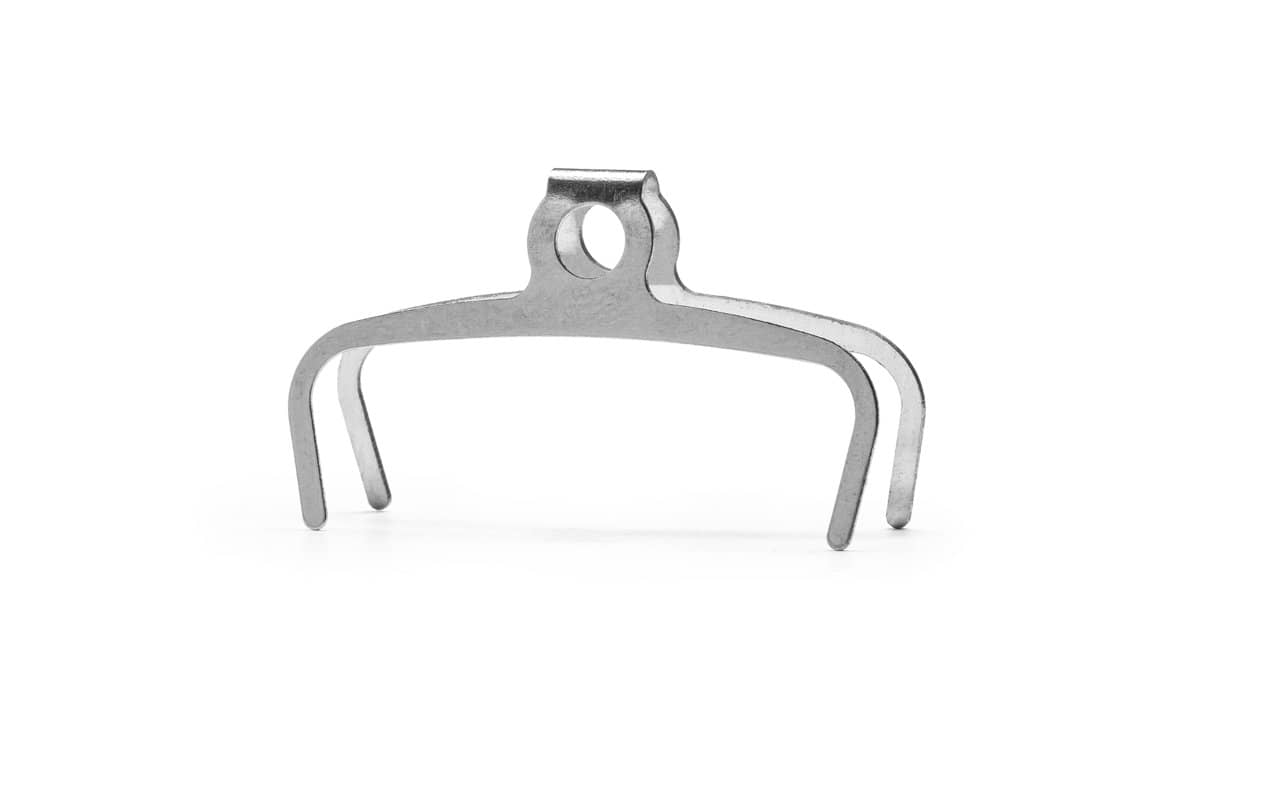
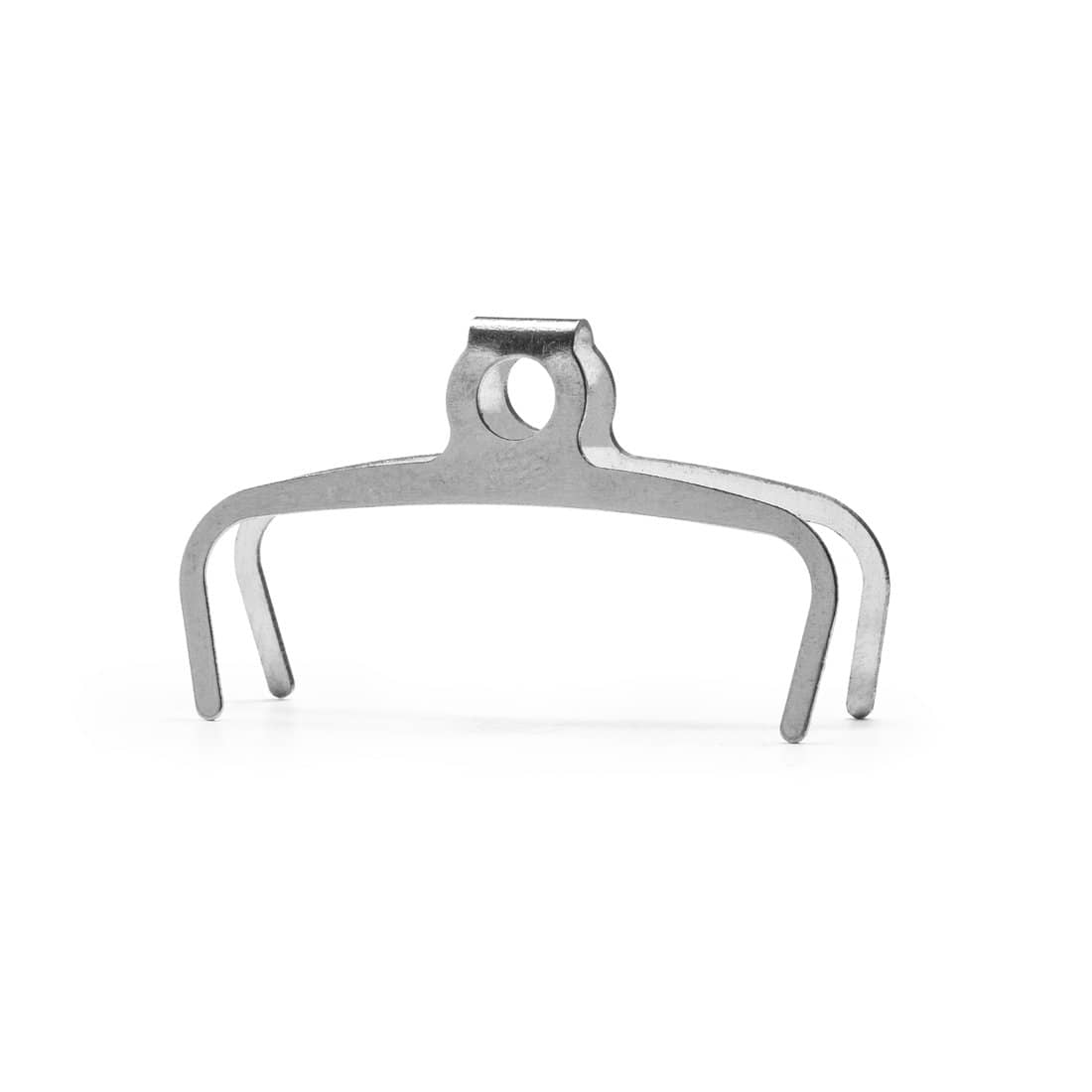
GRAPHENpads® World's best Disc Brake Pads. Disc 31 (G2)
Don't wait, order 2 sets per bike.
Thanks for your rating.
Do you like this product? Share it with your friends!
GRAPHENpads® - the new era of braking confidence and consistency is here.. Ceramic GRAPHENpads® are a completely new benchmark for the braking pad industry thanks to our unique approach to the design of backplate cooling fins, bespoke backplate coating with graphene as well as a completely new friction compound, which uses specially modified graphene instead of toxic copper. These pads fit Sram G2, Guide brakes and more. GRAPHENpads® Won the prestigious IF DESIGN AWARD 2023.
Mass (+/-1g): |
26g per set + 1g spring |
Compatibility |
SRAM G2 Ultimate, RSC ; Guide Ultimate, RSC, RS, R, T ; Avid XO Trail, Elixir 9 Trail, Elixir 7 Trail, Trickstuff Direttissima (C42 caliper), Piccola HD (C42 caliper only) |
Composition |
Ceramic organic Performance friction compound containing graphene. Thermal coating containing graphene. We don't use copper or any heavy metals |
Usage |
All weather conditions |
In the box |
Two pads (set per wheel), one spring. Packed in reusable aluminium can |
Even though our pads provide excellent performance and lifespan in all conditions, when cycling for a prolonged time (winter season for example) in very bad and highly abrasive conditions (thick mud, grit, wet sand) their lifespan will be reduced. We use an organic-ceramic base friction compound which by definition wears faster than a metallic friction compound.
The product
Brake pads are the single most important part of the bike, which determines how confidently you can descend. The key element to their optimum performance is to keep the temperature of the brake pads and the rotor as low as possible (ideally below 400C), especially on longer descends. The hotter the pads get, the faster they fade, which means they lose the ability to slow you down reliably when needed. Overheated pads lose braking consistency and behave differently each time you press the brake lever, which greatly diminishes your braking confidence, effectively making you ride much slower. This is why Shimano introduced cooling fins to disc pads in attempt to lower their operating temperature.
The ideal brake pad will have the same predictable braking power, initial braking bite and perfect modulation throughout a long descend. After 3 years of development, we believe that we have achieved just that with our GRAPHENpads®. The results of the machine tests and thermal imaging show that we were able to reduce disc pad and rotor temperature by up to 35% vs competitors and completely eliminate brake fading.
Rotors are heated repeatedly to high temperatures exceeding 500°C, increasing the danger of softening of the rotor materials by tempering. Temper softening causes increase of wear and warping of the rotor and leads to reduced brake performance. For this reason it is extremely important to evacuate heat from the rotor-pad interface as fast as possible.
The key elements of GRAPHENpads®
*First pads on the market containing specially modified graphene in their friction compound, which greatly improves braking performance, durability and heat transfer to the backplate.
* Thanks to the backplates being entirely covered in graphene heat dissipating coating, it was possible to achieve much greater heat transfer from the friction material to the cooling fins and at the same time, increase radiation of heat (IR spectrum) by over 20% (which is very significant).
* Very thin fins structure for superior airflow and cooling. They have significantly greater airflow compared to traditional radiators that increases convective heat dissipation.
* To date, GRAPHENpads® are the only brake pads in the market that completely eliminate toxic copper, ahead of new regulations (copper brake dust is proven to be toxic to aquatic life hence new California regulation will ban use of copper from 2025)
* Graphene in disc pad friction material prolongs the life of rotors by embedding graphene particles into micropores of the rotor braking surface.
* They are produced in EU unlike majority of other pads on the market, which come from a single Taiwanese factory.
What you will feel
* Predictability and power, allowing you to regain full control of your braking
* Better modulation and faster stopping
* Improved confidence when descending
* No brake fade, more consistency and reliable braking feel corner after corner, even on the most demanding descends.
* They are very quiet, even during long descends.
* They reduce fatigue of your hands due to greatly reduced brake lever force needed to achieve powerful braking compared to competition.
Why the majority of pads have similar average performance
The great majority of popular organic disc pads on the market are produced by just one Taiwanese company. Interestingly, they don’t develop braking compounds themselves but instead, source such formulas from elsewhere. Anyone can pick their braking compound from a short catalogue, then pick a color of the backing surface and just like that, they’ve created their own brand of braking pads.
GRAPHENpad’s friction compound on the other hand, was developed with help from renowned European disc pads specialist with decades of experience and one-of-a-kind equipment, that allows for precise performance testing. Graphene is still a very new material, especially in friction brake compounds. Due to its very unique properties and years of testing, we were able to develop a friction material like no other. In the automotive industry, where every major car maker has already filed several patent applications for friction compounds containing graphene, it’s clear to see that it is the future of braking pads. New regulations which start from 2025 will prohibit the use of copper powder in disc pads. Graphene is not only an excellent substitute to copper, but a major upgrade in terms of performance. We are the first company in the bicycle industry offering graphene in the friction compound.
Descending test
In this testing sequence lasting 600s (10 min) and using a one-of-a-kind machine, we performed a simulation of a long descent on a road bike, with a constant force of 10N on the brake lever and slope angle of 12,5%. Velocity was 25km/h (15.5mph) with air blowing on the braking system at the same speed. Key parameters were recorded at 0.1s interval (6000 points per test). This test helps us to understand how the brake system and friction material behaves during longer periods of braking and when the brake is subjected to fading.
In simple words we simulate a 100kg (220lbs) rider+bike gently dragging their brakes all the way down the descend. It is a typical behaviour for unexperienced riders when descending in alpine terrain.
We have compared GRAPHENpads to Shimano K-Type L03A (Dura-Ace), Swissstop Disc 34 RS and Kogel R9100 BIA (sintered with copper) pads. In every brake pad test we have used a new Dura-Ace rotor 160mm, new 105 caliper and new brake oil. Those control measures are important as once the caliper reaches over 450C, its seals sustain permanent damage and decomposition of braking fluid can occur. When temperature of the rotor goes above 500C, aluminium core in the rotor starts to soften, causing permanent deformation of the braking surface. Each test was conducted following a standardised bedding-in process of the brake pad-rotor pair, with automated cycle of 100 braking events in dry, 30 in wet, 30 in dry conditions and various, pre-set intensities. Then we let the system to cool down to ambient temperature and dry out before main test.
Our machine tests and thermal imaging show that with GRAPHENpads® (Graph 1), it is possible to reduce disc pad and rotor temperature by up to 35% vs competitors and completely eliminate brake fading. It is also worth noting that friction coefficient remains very stable, which translates to very predictable and consistent braking performance.
GRAPHENpads® Descending test
Shimano K-type L03A Dura Ace pads Descending test
Swissstop Disc 34 RS pads Descending test
Kogel R9100 BIA pads Descending test
From thermal imaging we can conclude that GRAPHENpads® were able to significantly reduce brake caliper temperature vs other brake pads, which translates to increased performance and prolonged life of caliper seals and braking fluid. (In images below dark violet represents temperatures of around 27C and “white” represents over 400C )
Progressive braking test
In this testing sequence lasting 300s (5 min) and using a one-of-a-kind machine, we performed a simulation of a series of braking cycles at various brake lever forces. This test helps us to understand what is happening in the first 20 seconds after the brake lever is engaged.
Flywheel connected to the brake rotor was constantly spinning at 25km/h (15.5mph) while brake lever force of 14.5-20.5N was applied at 1N increment in 7 consecutive cycles lasting 20s each, followed by 20s with brake lever disengaged to cool down. Air was blowing on the braking system at the same speed as rotor speed to simulate wind. Key parameters were recorded at 0.1s interval (3000 points per test). We have compared GRAPHENpads to Shimano K-Type L03A (Dura-Ace), Swissstop Disc 34 RS and Kogel R9100 BIA pads. We used the same bed in procedure as in the Descending test.
Looking at the velocity of rotor (blue lines) on the graphs, which represent the ability of brake pads to slow down the bike at certain brake lever force, it is clear that GRAPHENpads possess superior braking performance at lowest possible brake lever forces. This means that when using GRAPHENpads, far less force has to be applied to the brake lever to stop the bicycle, in a significantly shorter time when compared to the competitors. Effectively you can descend faster and brake later with very small lever force required.
On the graph above GRAPHENpads completely stopped the flywheel (rotor velocity to 0) on already second braking cycle which interestingly lasted less than allocated 20s. Each subsequent braking cycle (yellow bars) lasted even shorter because flywheel was completely stopped much faster than anticipated. The faster the brake pads can stop the rotor the lower the temperature of the system is (red line) because there is no time for the heat to build-up.
On the graph above Shimano Dura-Ace L03A pads completely stopped the flywheel on sixth braking cycle (blue line). It also seems that backplate cooling fins helped to decrease the temperature (red line) during each subsequent braking cycle despite each lasting full 20s.
On the graph above Swissstop Disc 34 RS pads didn’t stop the flywheel (blue line) during the testing sequence. The progressive reduction of the flywheel speed during each consecutive cycle suggest, that bigger force would be required on the brake lever to stop it completely.
On the graph above Kogel R9100 BIA pads didn’t stop the flywheel (blue line) during the testing sequence. The flywheel speed was not reduced during any of the braking cycles, this suggests that significantly bigger force would be required on the brake lever to stop it completely. Interestingly we can also observe a temperature build-up in the system, which was not observed in other pads. Test was performed twice.
Why cooling fins are the critical part of brake cooling ability.
In order to explain how important the disc pad fins are to overall disc brake cooling abilities, first we need to understand what is the most important factor that helps the brake caliper, rotor and pads to cool down. Air moving past all braking elements during the ride, plays this crucial role. Increasing the surface of disc pad backplate enables more exposure to wind hence improves cooling. The cooler the pads, rotor and caliper, the better the braking performance.
In the thermal images below, you can see GRAPHENpads® tested with and without air blowing on the test setup. It is clear that without the wind, even the best brake pads start overheating very fast, showing the importance of cooling fins in overall temperature management and braking performance.
But graphene is used in super low friction lubricant…
In order to understand why graphene is such a good material for friction compound, one needs to understand how friction compound is made. Typical organic friction compound includes five classes of components: a fibrous material made from inorganic/organic/metallic fibers (like copper), a binder (like thermosetting polymer), a "filler" (various soft ceramic powders), one or more lubricants/friction modifiers (like graphite, copper), one or more abrasives (hard ceramic powders). The binder, which is typically a phenolic resin that bonds all components together, has a very high friction coefficient, therefore it is necessary to add friction modifiers/lubricants to lower the friction coefficient and allow braking modulation.
Copper is a great example of a material that not only acts as fibrous material but it is also a lubricant and conductor of heat to the backplate. Graphene on the other hand is several times stronger than copper, conducts heat 3-6 times better and its coefficient of friction is several orders of magnitude lower. By eliminating copper and finding the right balance of graphene and other components, we created one-of-a-kind friction material that delivers extraordinary performance.
How to Install GRAPHENpads
Please bed the pads in for proper braking experience. This is CRUCIAL part of every brake pad installation. Neglecting this step will produce sub-par experience.
1. Remove wheel and old brake pads.
2. Use a brake cleaner to clean inside of the caliper and the rotor surface (alternatively use isopropyl alcohol)
3. Gently push each piston back into the caliper body (using for example big screwdriver). Then mount new pads and spring
4. Most important part - While riding at about 20km/h (12mph) in safe environment, apply brakes evenly until speed drops to walking pace. Repeat 20 times. Then stop 10 times aggressively
For more detailed instruction please watch the video
If you have Sram Guide brakes that are older than 2016 model, you will have to cut part of the fin structure with pliers as illustrated on the picture below. Fin structure is already pre cut for easy procedure. Please remember you need to cut one pad on one side and the other pad on the opposite side.
Share your Oval chainring photos with us on Instagram: #OvalThis #absoluteBLACK #OVALREVOLUTION
Designed in England. Manufactured in EU.
Graphenpads® is a registered trademark of absoluteBLACK®. GRAPHENpads® design is protected by several granted design patents and several patent pending applications.